Exploring the World of Plastic Molding Tools: A Guide for Metal Fabricators
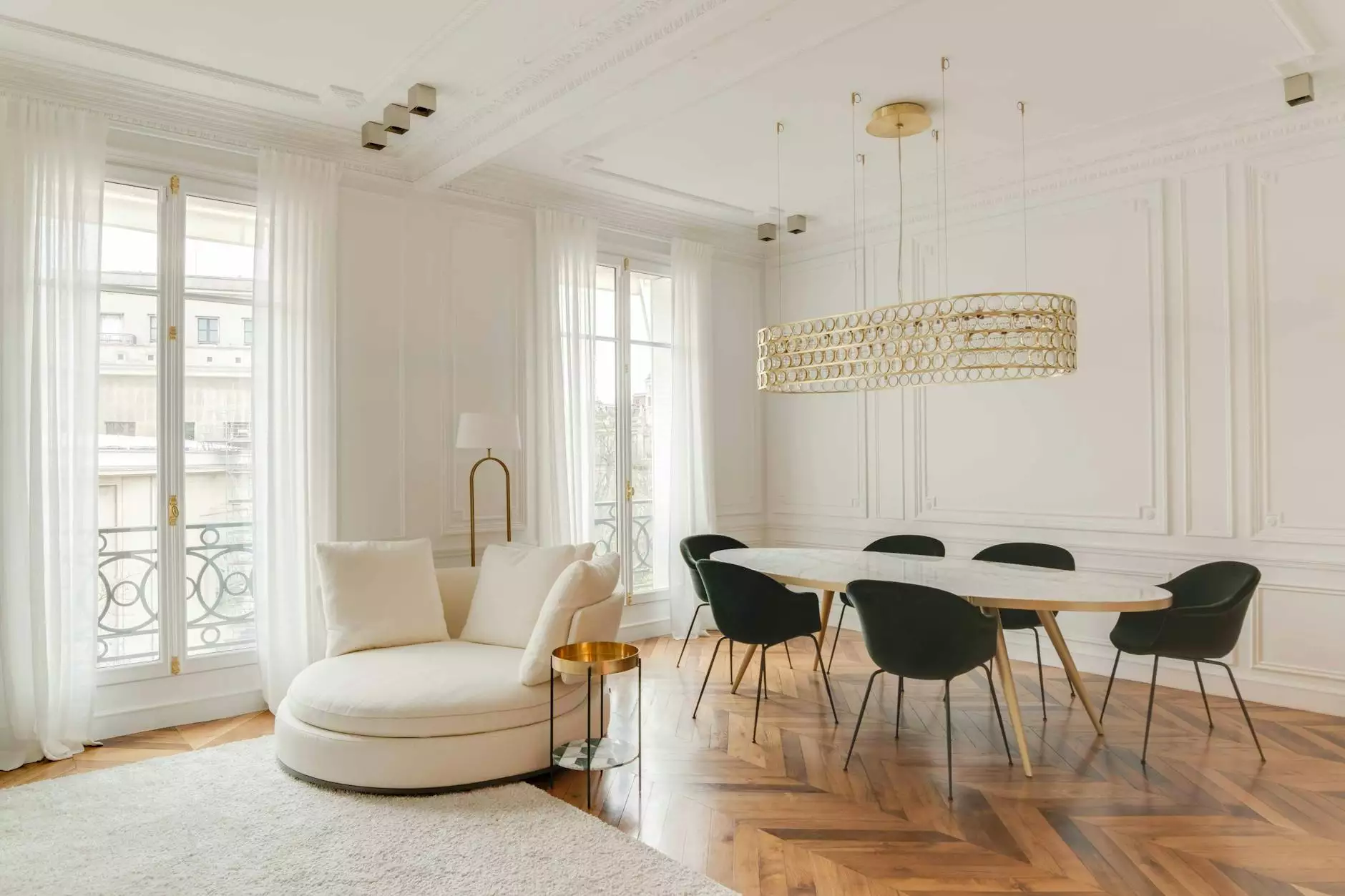
In the ever-evolving landscape of manufacturing, plastic molding tools have emerged as one of the cornerstones of production processes across various industries. For metal fabricators, understanding the nuances of these tools is crucial in enhancing not only the efficiency of operations but also the overall quality of products. This comprehensive guide will delve deep into the world of plastic molding tools, examining their importance, applications, benefits, and how they can significantly optimize your manufacturing processes.
The Importance of Plastic Molding Tools in Manufacturing
Plastic molding tools play a vital role in shaping the direction of the manufacturing industry, especially for metal fabricators who often integrate plastic components into their metal products. The following points highlight their significance:
- Versatility: Plastic molding allows for a wide range of shapes and designs that can be tailored to specific needs.
- Cost-Effectiveness: Manufacturing with plastic is often more affordable compared to other components, saving businesses money in the long run.
- Durability: Modern plastics are engineered to provide strength and resilience, making them ideal for various applications.
- Sustainability: Many plastic molding tools are designed with eco-friendly practices in mind, allowing businesses to reduce their carbon footprint.
Types of Plastic Molding Tools
Understanding the different types of plastic molding tools available can help businesses choose the right ones for their operations. Below are the main categories:
1. Injection Molding Tools
Injection molding is one of the most common processes for creating plastic parts. This method involves injecting molten plastic into a mold, allowing for precise shapes and intricate designs. Key features include:
- High Production Rates: Ideal for large-scale manufacturing due to its speed and efficiency.
- Precision: Capable of producing complex geometries with high tolerances.
- Material Variety: Compatible with a wide range of plastics, including thermoplastics and thermosets.
2. Blow Molding Tools
Blow molding is used primarily for creating hollow plastic objects, such as bottles. The process involves inflating softened plastic within a mold. Features include:
- Cost Efficiency: Particularly economical for high-volume production.
- Lightweight Products: Excellent for producing lightweight yet sturdy containers.
- Custom Shapes and Sizes: Offers flexibility in creating various container designs.
3. Compression Molding Tools
This technique is primarily used for producing large, bulky parts. Compression molding involves placing plastic material in an open mold cavity, closing the mold, and applying heat and pressure. Key benefits include:
- Cost-Effective for Large Parts: Especially suitable for bulkier products, reducing material waste.
- Durability: Produces strong and resilient products, perfect for industrial applications.
- Low Tooling Costs: Compared to other molding processes, compression molding often has lower initial costs.
Key Benefits of Utilizing Plastic Molding Tools
The adoption of plastic molding tools offers numerous perks, especially for businesses seeking to enhance their manufacturing processes:
1. Increased Productivity
With the ability to produce multiple parts simultaneously, plastic molding techniques can significantly increase overall productivity. Automated processes reduce human intervention, leading to higher efficiency. This means that orders can be fulfilled faster, giving businesses a competitive edge.
2. Enhanced Quality Control
Modern plastic molding tools are equipped with advanced technology that allows for real-time monitoring and adjustments during the manufacturing process. This ensures consistency in product quality and minimizes defects, leading to greater customer satisfaction.
3. Innovation in Design
The versatility of plastic molding tools opens up endless possibilities in design. Metal fabricators can collaborate with product designers to create innovative solutions that meet the needs of their customers. Incorporating unique plastic components can also enhance the functionality and aesthetics of metal products.
4. Environmental Advantages
As manufacturers face increasing pressure to adopt sustainable practices, plastic molding can contribute to greener operations. Many modern plastics are recyclable, and innovative techniques minimize waste during production. Furthermore, businesses can explore bio-based plastics as an alternative to traditional materials.
Integrating Plastic Molding Tools into Your Fabrication Process
For metal fabricators interested in integrating plastic molding into their workflow, here are some strategies to consider:
1. Collaborate with Experienced Suppliers
Finding suppliers who specialize in plastic molding tools is essential. These partners can provide insights into the best materials and techniques suited for your projects. Building strong relationships with suppliers allows for smoother operations and better-quality products.
2. Invest in Training and Development
Ensure that your workforce is adequately trained in the operation and maintenance of plastic molding tools. Offering ongoing education will keep your team updated on the latest techniques and technologies, boosting overall productivity and ensuring high-quality standards.
3. Implement Quality Assurance Protocols
Establishing strict quality control measures is crucial when introducing new processes. Regular inspections and testing of molded parts can help identify issues early on, preventing costly production delays and maintaining customer satisfaction.
4. Monitor and Optimize Production
Utilize data analysis and monitoring systems to track the efficiency of your molding processes. This analysis can reveal bottlenecks and areas for improvement, ensuring that your operations run as smoothly as possible.
Challenges and Considerations
While the benefits of plastic molding tools are significant, it's essential to be aware of potential challenges:
1. Initial Investment
Acquiring advanced molding equipment can represent a substantial upfront cost. However, this investment is often offset by long-term savings in production costs and waste reduction.
2. Material Compatibility
Not all plastics are suitable for every application. Understanding the properties of different materials is crucial in ensuring that the end products meet the required specifications.
3. Regulatory Compliance
Manufacturers must stay abreast of regulations concerning plastic materials, especially in industries such as food packaging or medical devices. Ensuring compliance is vital to avoiding costly legal implications.
Future Trends in Plastic Molding Tools
As technology continues to evolve, the future of plastic molding tools looks promising. Here are some trends to watch:
1. Automation and Industry 4.0
The integration of smart technologies and automation into molding processes is on the rise. Industry 4.0 will enable manufacturers to significantly enhance productivity while ensuring quality control.
2. Sustainable Materials
Demand for eco-friendly materials is increasing. Innovations in biodegradable and recyclable plastics will drive the development of more sustainable molding processes.
3. Advanced Mold Design
As computer-aided design (CAD) and simulation technologies advance, the ability to create more complex molds with precision will become increasingly feasible, allowing for enhanced product features and performance.
Conclusion
In conclusion, plastic molding tools are an indispensable asset for metal fabricators looking to modernize their operations and adapt to the changing landscape of manufacturing. By understanding the various types of molding tools, their benefits, and strategies for integration, businesses can enhance their production capabilities, drive innovation, and improve their sustainability footprint. By embracing these practices, metal fabricators can not only fulfill current demands but also prepare for future challenges and opportunities in an ever-competitive market.
For more information on the vast array of plastic molding tools and how they can benefit your operations, consider consulting industry experts or visiting resources like deepmould.net.